Open-source fabrication process for creating smart textiles
PolySense adds electrical functionality to everyday fabrics.
The fabrication process we developed is perfect for on fabric augmentation, and uses tools you can find in any kitchen.
The PolySense project was born in DataPaulette, pushed by my friend Cedric Honnet. The HCI work was conducted at Saarland HCI with Paul Strohmeier and Bruno Fruchard, during a series of research visits by Hannah Perner-Wilson (KobaKant) and Cedric.
Additional material can be found on the website http://counterchemists.github.io/
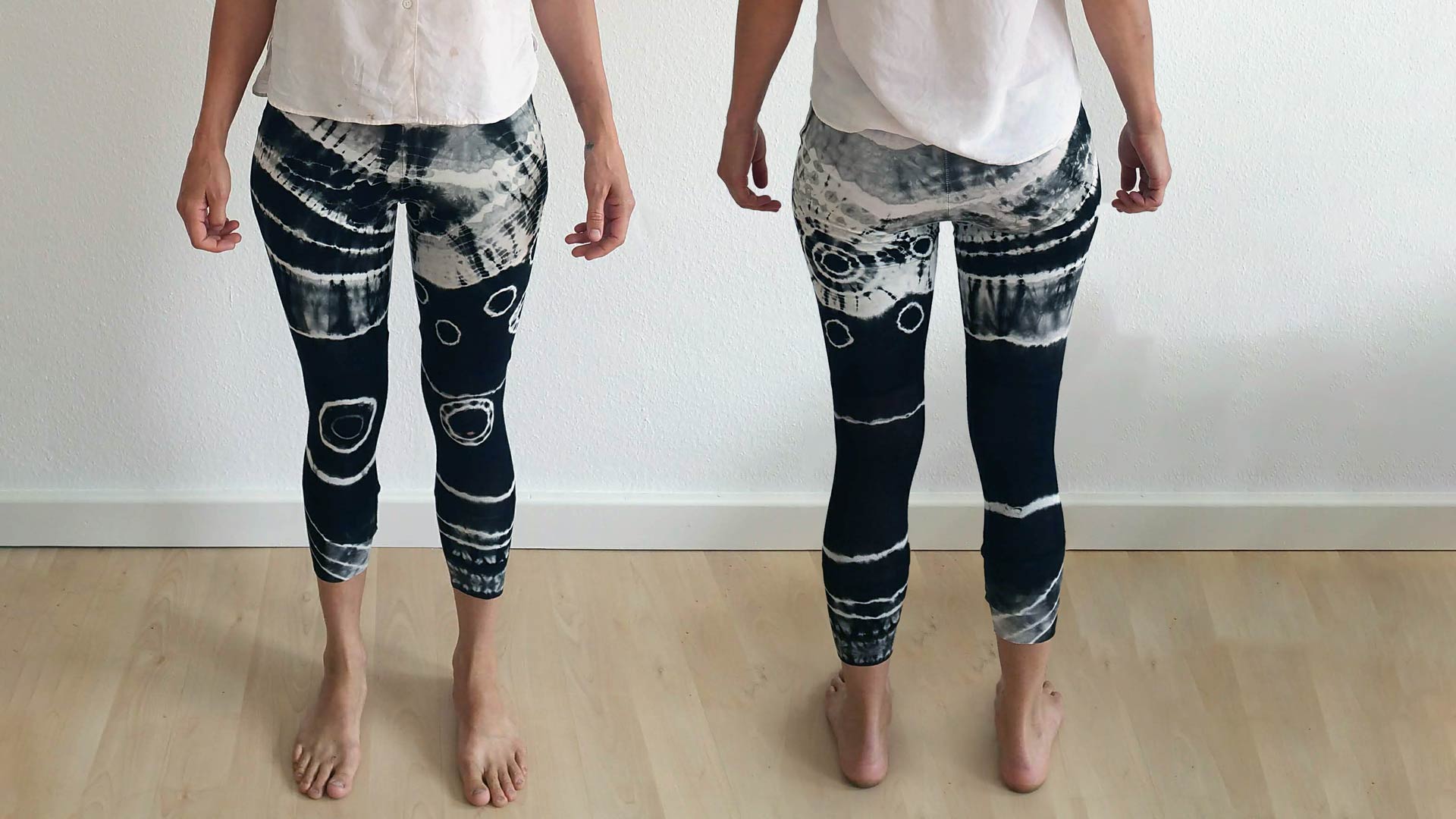
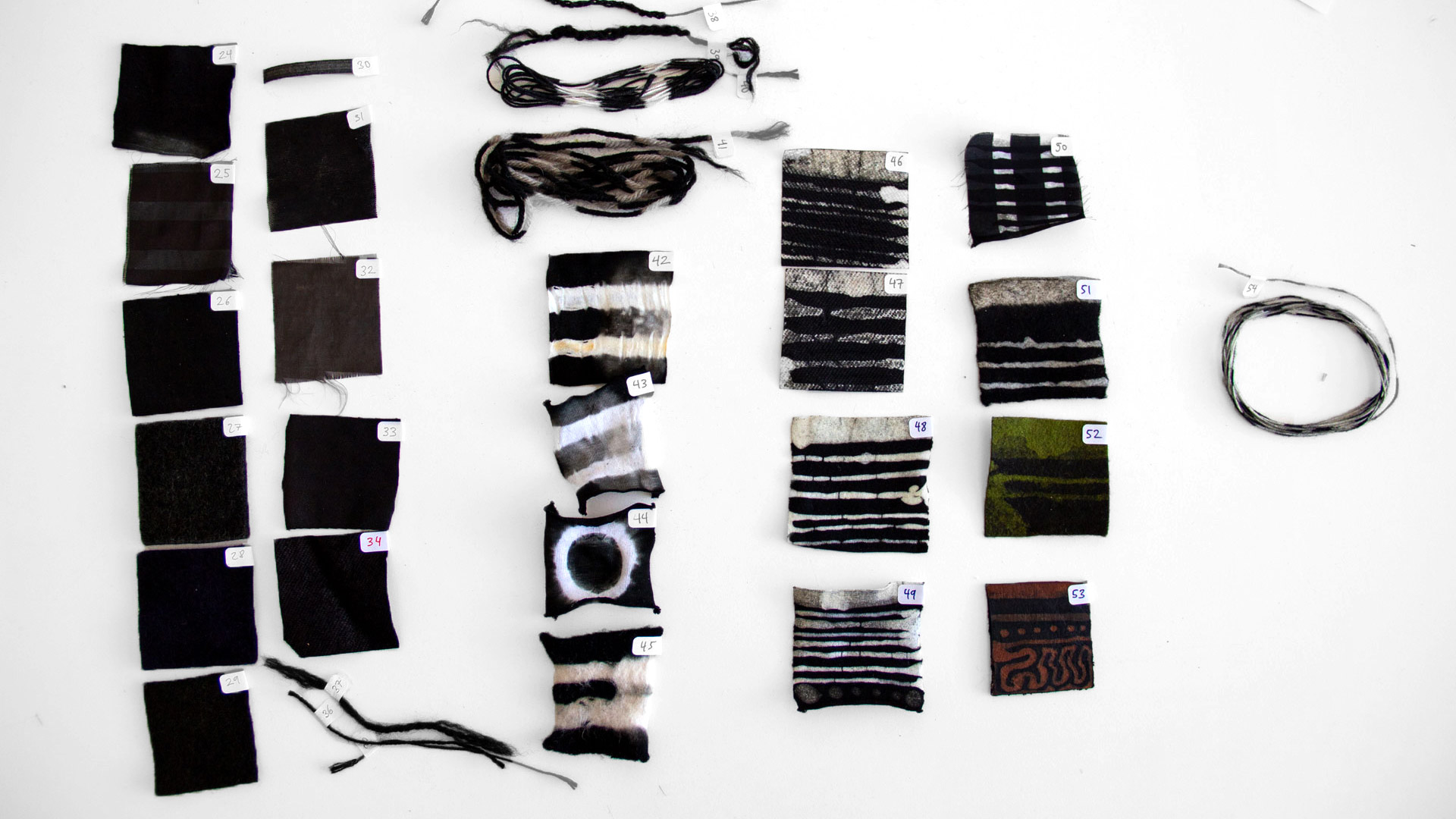
New process makes fabric smarter
There are many ways of creating custom textiles, rooted in age-old traditions. For example, the colourful tie-dye motives of the sixties can be traced back to ancient Japanese shiburi. If you wish to create custom patterns, finding the tools and information to use them is easy.
Functional fabrics -- also known as smart fabrics or eTextiles -- have no such traditions. Instead one relies on expert knowledge or factory-produced materials. If lay-person wishes to create a custom functional fabric, most people would not know where to start.
With this project, we intend to make the creation of smart fabrics as accessible and easy to perform as creating a tie-dyed T-shirt.
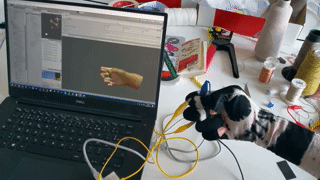
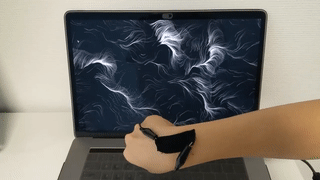
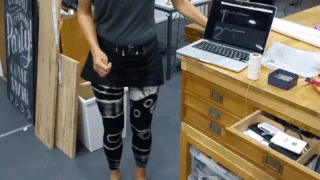
How does it work?
PolySense uses a process called in-situ polymerization. This can be thought of as a dying process: one soaks a fabric in a chemical “dye” and when the fabric is removed from the fluid, it is electrically conductive.
However, this is not a regular dye. During the dyeing process, a chemical reaction happens, after which each individual fibre of the textile is completely wrapped in chains of conductive polymer. This is called polymerization. "In-situ" means that the polymerization occurs within the fabric, at the place where one intends to use the resulting functional properties. This is radically different from existing DIY approaches, such as coatings, which apply a layer to the fabric, rather than the individual fibres, or literal stacking of fabric, where functional fabric is sewn or bonded on to non-functional materials.
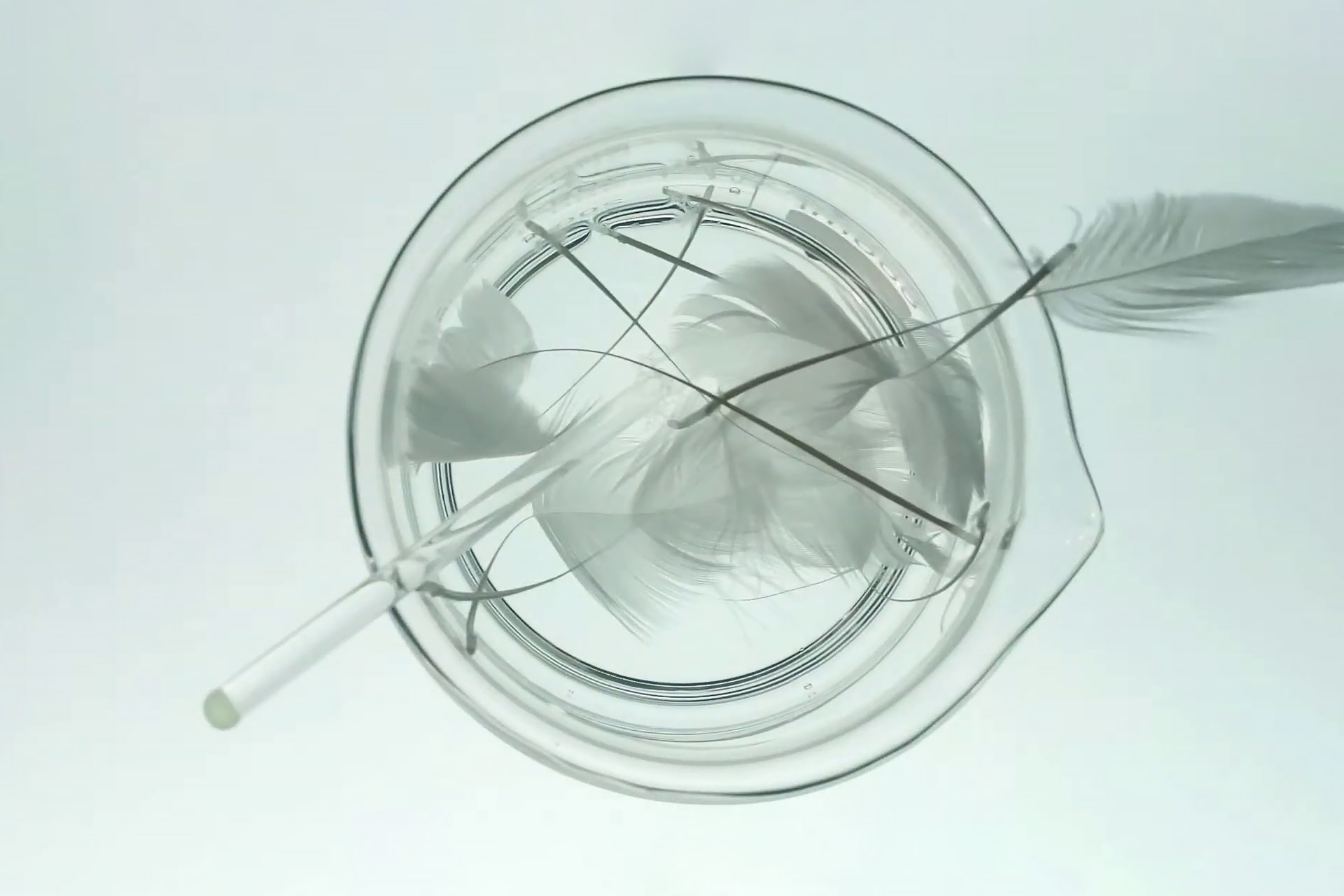
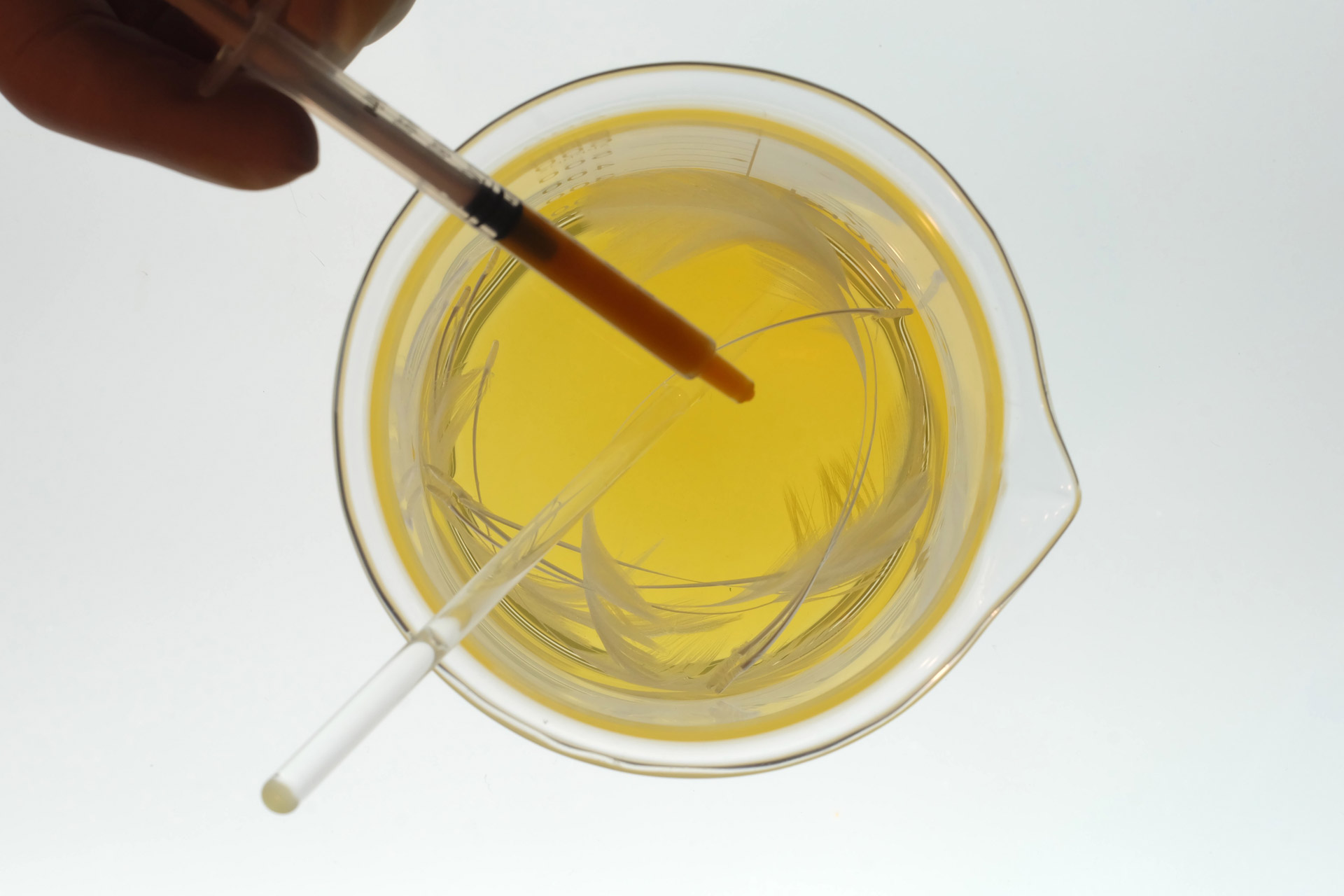
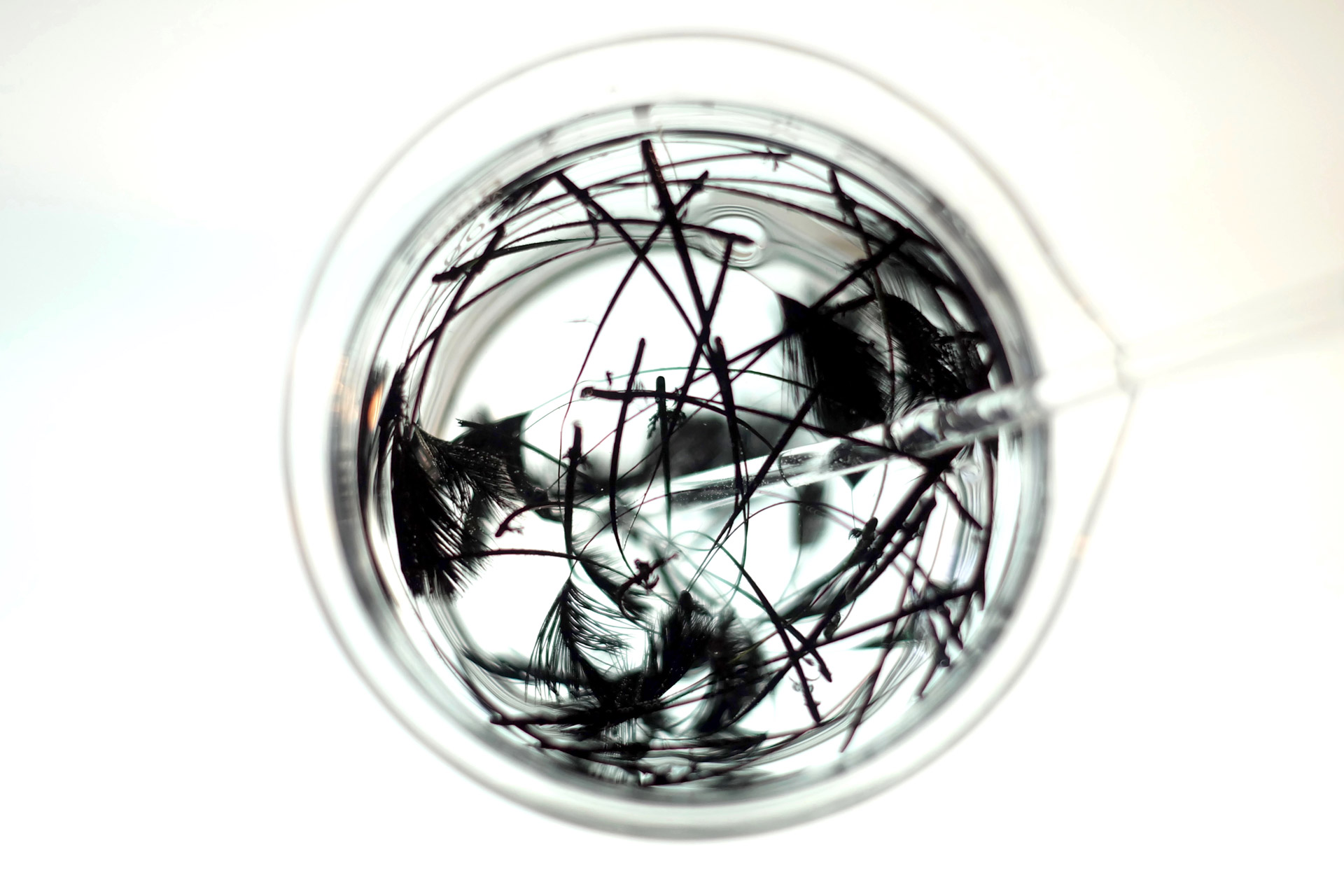
Project Stymphalian Birds by Audrey Briot using Polymerization process. Pictures credit to Audrey Briot.
The process is easy to reproduce and can be completed in under an hour: First, the textile is soaked in a mix of water and Pyrrole for 10 minutes. Then the polymerization is initiated by adding Iron Chloride. Finally, the textile is stirred in this bath for about 30 minutes until polymerization is complete. This can be done in a small bowl, with a hand mixer, or in a washing machine, for larger quantities.
Why is this process so exciting?
Creating one’s own functional textiles means that one can freely experiment without the constraints of prefabricated materials.
1. PolySense offers freedom of material.
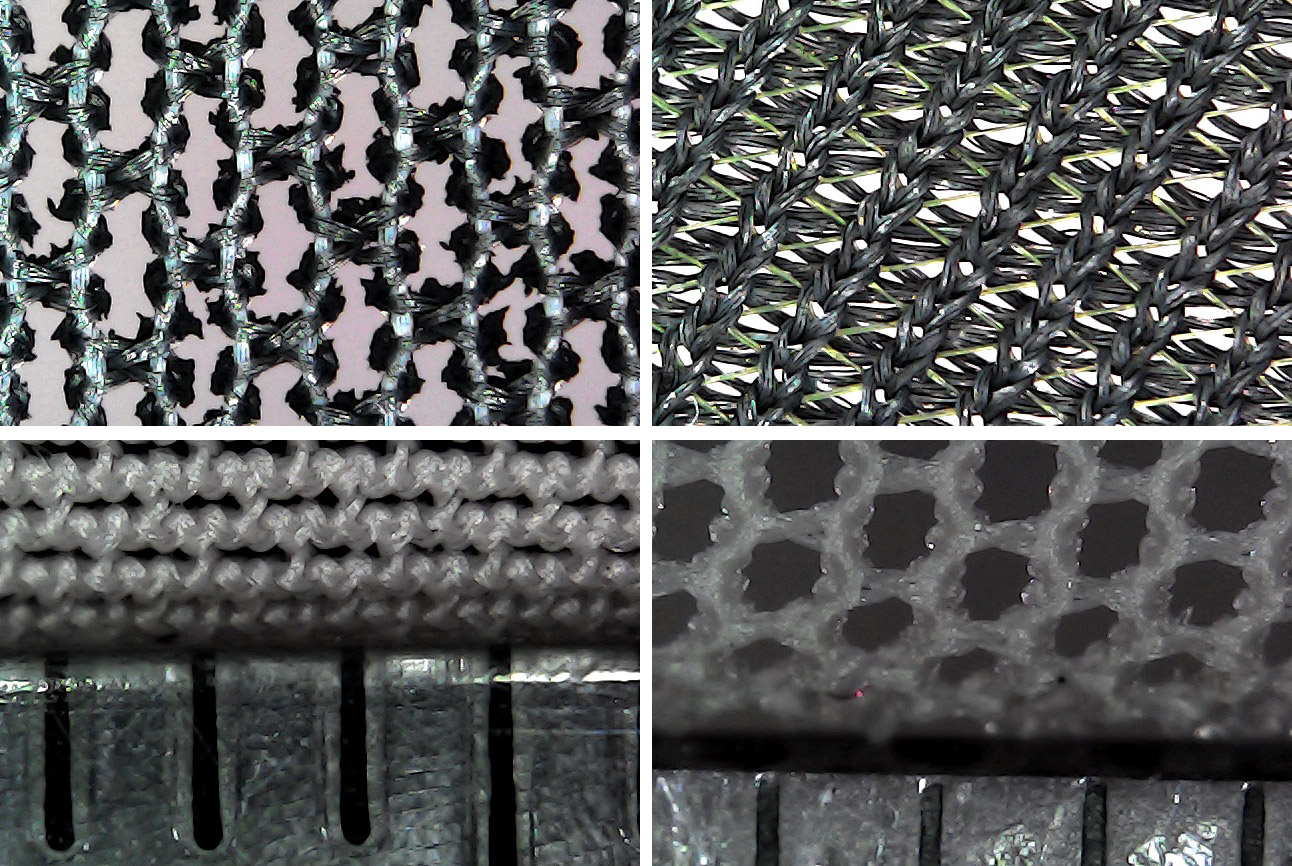
When developing new smart clothes, makers and researchers are limited in their choices of conductive bought materials. These materials have specific physical and mechanical properties that do not necessarily fit all purposes. For instance, one might want a fabric stretchable and thin, while another prefers a thicker and more comfortable one. Because PolySense enables functionalization of existing fabric, it broadens the range of conductive fabric which can be used to an unlimited number of choices.
Polymerization also broadens the range of interactive objects which can be created. One might augment existing objects, such as adding sensing abilities to one’s favourite backpack. One can also create items with completely new and unexpected behaviours by polymerizing items with unique properties such as kinesiology tape, zippers or feathers!
2. PolySense relies on traditional processes

We highlight that polymerization can be thought of as a traditional dyeing process, just for creating custom electrical properties instead of custom colours or patterns. This enables the transfer of existing dye-based techniques to the creation of electrically functional textiles. For example, tie-dye, batik, or ikat can be used for creating electrical patterns and can support the implementation of complex electrical circuits.
We also show how to use etching on existing functional fabric to further customize it. The resulting custom fabric can be used as sensors, resistors or conductors and even whole circuits including sensing elements can be implemented in fabric.
3. PolySense is open
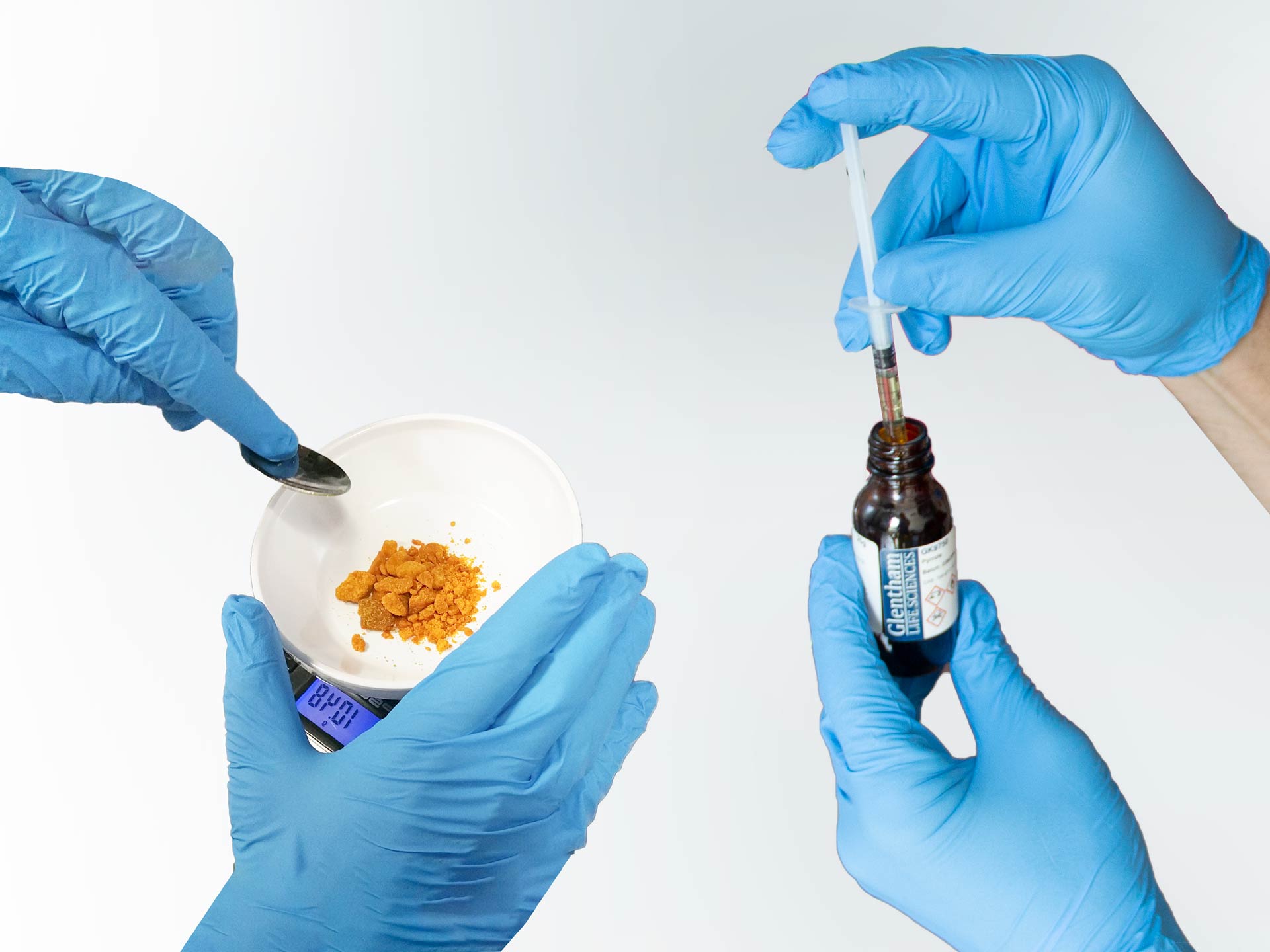
Existing piezoresistive materials act as a black box. They work, but manufacturers do not publish details on how they are made. As a result, it is difficult to understand how to push the boundaries of their performance, as one can only use those materials, which companies have the interest to produce.
This highlights yet another problem of closed products. Even if one can source them today, it is unclear if one can find the same material in the future. For example, a very commonly used piezo-resistive fabric recently changed its electrical properties, and now many online tutorials do not work. Another common material was temporarily taken off the market. This uncertainty makes it infeasible to use these materials in products.
PolySense addresses this problem by providing detailed open-source documentation and instructions: The process can be reproduced in any quantity, ranging from small amounts for personal use to large batch manufacturing for companies. The resulting fabric has equal sensing capabilities than commercial solutions.
How can these smart fabrics be used?
An application of PolySense is creating pressure or stretch sensitive fabric. This sensitive fabric can be used for measuring explicit input, for example, one could create a sleeve which one can use for gesture input, to control a smart environment. One could also create clothing for activity tracking, by measuring body pose.
One might also create heating elements, or temperature sensing elements or both at once. For example, one might create a jacket which measures the temperature and starts heating, only if the temperature falls beneath a certain threshold.
As almost any material can be treated with our method, new opportunities arise. For example, we have created functional sports-tape which one can use as on-body sensors or zippers, which can measure how far they are zipped.
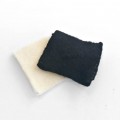
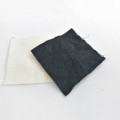
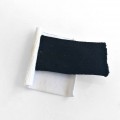
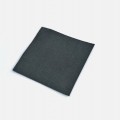
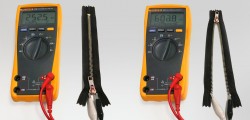
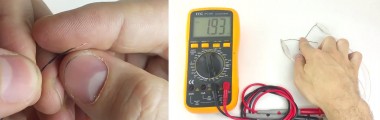
What are the research opportunities?
Other publications highlight specific pieces and technologies which are implemented using the process described in our paper.
For example, rapid prototyping of on-skin interaction, where kinesiology tape is polymerized with this process to create on-skin touch and motion sensors at Augmented Humans 2020. A hybrid art-piece which features polymerized feathers at Designing Interactive Systems 2020, by Audrey Briot.
Publication
PolySense: Augmenting Textiles with Electrical Functionality using In-Situ Polymerisation Cedric Honnet, Hannah Perner-Wilson, Marc Teyssier, Bruno Fruchard, Jürgen Steimle, Ana C Baptista, Paul Strohmeier CHI‘20: Proceedings of the ACM SIGCHI Conference on Human Factors in Computing Systems, ACM (2020); 04/2020 PDF ↵
Medias
PolySense - High resolution pictures
HACKADAY: Dyeing Fabric To Create Sensors
Textile Insight: Making PolySense of E-Textile